This marks the fourth installment in our series, dedicated to exploring the feasibility of a modular biopsy system. In this article, our focus shifts to fundamental motor control techniques: the Clark and Park transformations.
The core system comprises a primary control board built around Xilinx ZYNQ Ultrascale+ and servo satellite motor drives based on Xilinx ZYNQ-7000. The ultimate objective remains the precise control of a multi-jointed robotic system designed to manipulate a biopsy needle accurately to predefined target areas.
Motor Control Board: Clark And Park Transformations
Field-Oriented Control (FOC) involves managing the components of a motor's stator currents, represented as a vector in a rotating reference frame d, q, aligned with the rotor flux. The intricacies of this vector control system demand dynamic model equations, enabling the calculation and control of instantaneous currents and voltages. The PMSM motor's electric torque relies on the interplay between rotor currents and the flux wave generated by stator currents. To handle the unmeasurable rotor currents, an equivalent quantity, described in d,q coordinates, replaces them, aligning with the rotor flux.
The Clarke transform translates three-phase currents (a, b, and c) into two-phase orthogonal stator axes (i-alpha and i-beta).
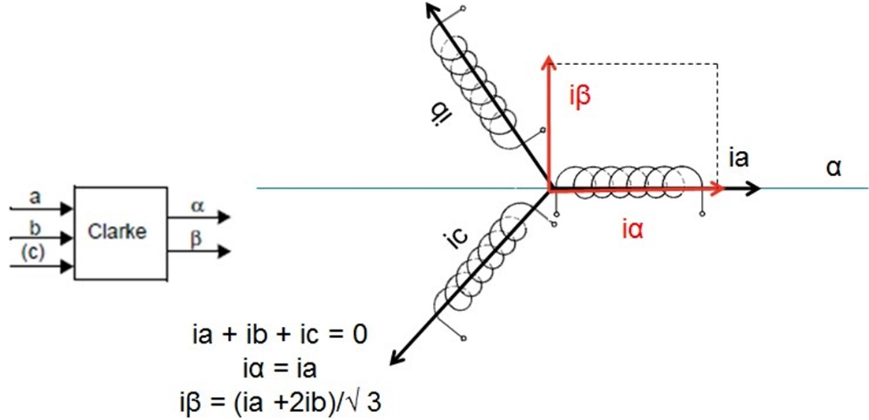
These two currents in fixed stator phase coordinates undergo transformation into ISD and ISQ currents components in the [d,q] rotating frame through the Park transform, employing the electrical rotor’s angle from the Absolute Encoder SSI-BISS module.
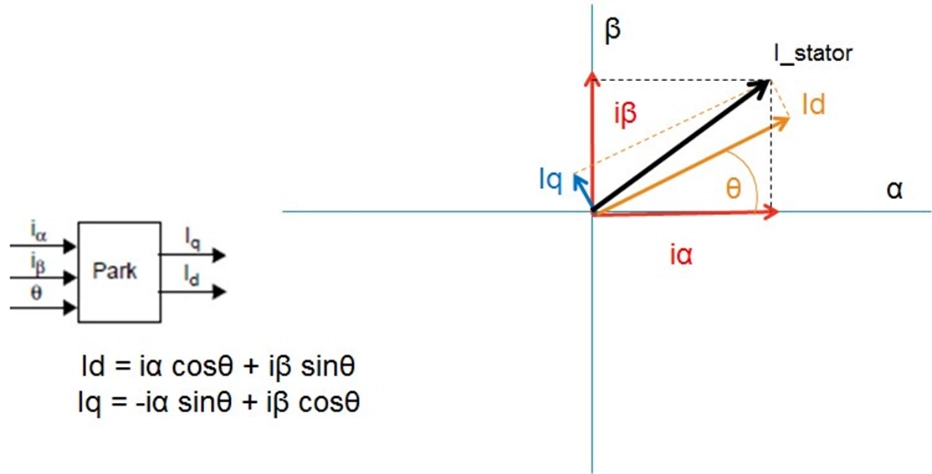
Proportional-Integral controllers regulate the variance between the desired torque and flux, maintaining the motor in the 90-degree magnetic/electric relationship. Post PID control, the inverse Park’s transform reverts Id, Iq values into Vα and Vβ stator voltages, feeding the PWM Space Vector Modulator.
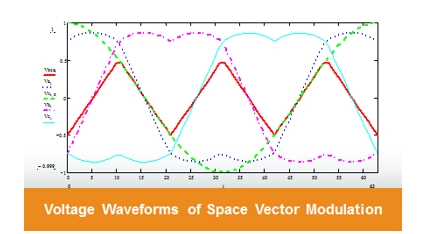
The SVM modulator produces a waveform resembling a pudding shape, instantaneously creating a homopolar structure on motor currents, resulting in sinusoidal flow. Figure 16 illustrates standard sinusoidal modulation, utilizing up to 86% of the DC_Link (yellow zone), while SVM allows up to 100% (red zone) before transitioning into non-linear motor movement.
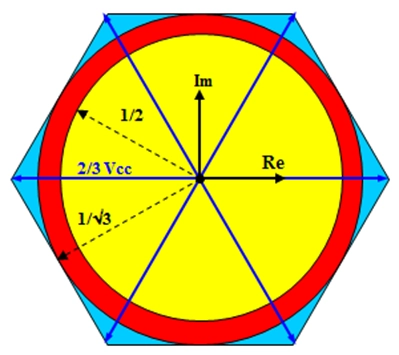
The power stage, depicted in Figure 17, integrates Gate Drivers, Mosfets, current sensors, and ADCs, configured for the 3-phase system.
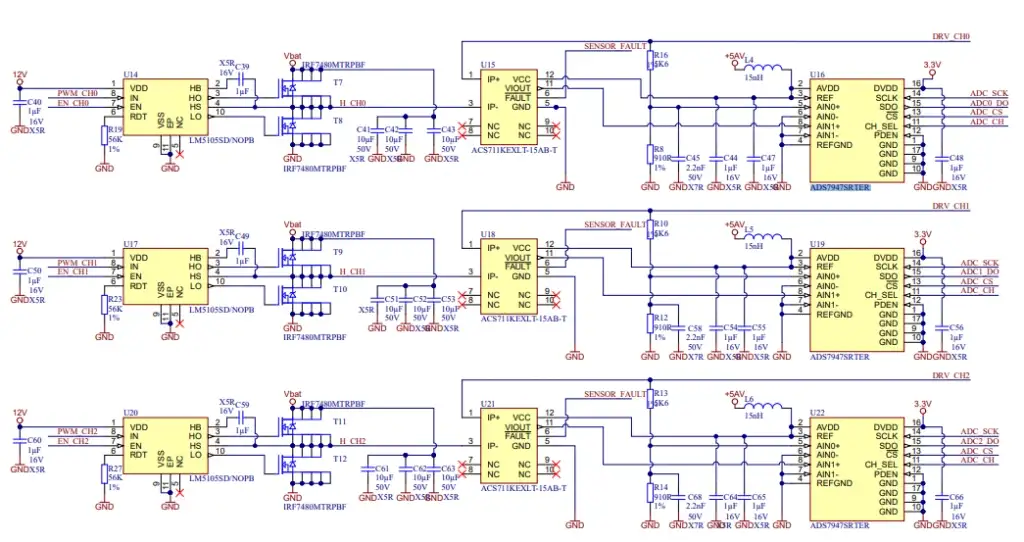
Motor Connection Configurations:
Two primary configurations, DELTA and WYE, define three-phase motors. DELTA connections are preferred in cases of limited available voltage, commonly employed in medical applications. WYE connections, prevalent in industrial setups, are also compatible with this application.
Absolute Encoder with SSI Interface for Transformations
Synchronous Serial Interface (SSI) serves as the standard serial interface for rotary encoders in industrial applications. Employing differential signaling (CLK and DTA) based on RS-422 standards enhances resistance to electromagnetic interference, crucial in industrial environments.
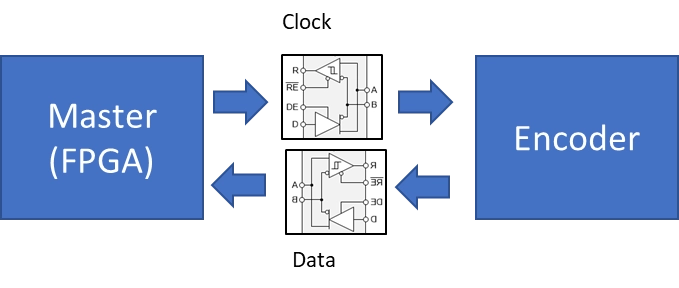
SSI Data, transmitted with the most significant bit (MSB) first, consists of 13 bits for angle transmission within one revolution (single turn). Multi-turns are also supported.
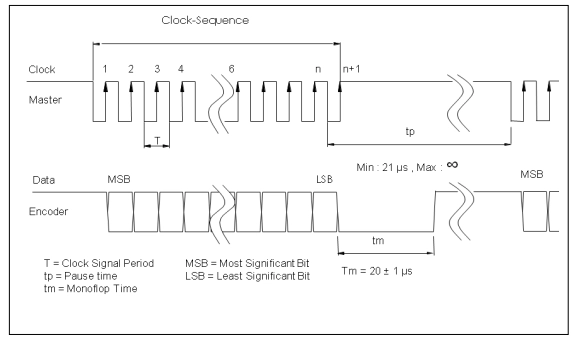
The figure below ring shift transmission, enhancing data safety by repeating the same data word. Various failure modes are meticulously addressed, ensuring protocol adherence and system safety.
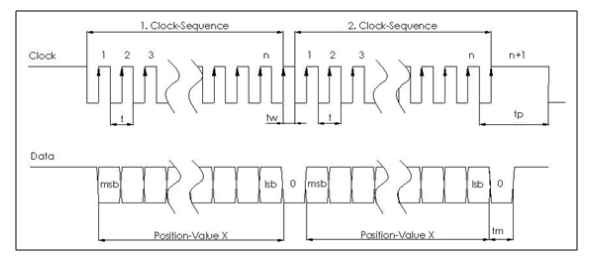
Would you like to know more about the intricacies of the Clark and Park transformations?
Contact our team to learn more at www.mklabs.ai